How a small sleeve can make a big difference – and how we can save up to 35% on article costs with our expertise.
In medical technology, every detail counts. Components must not only be manufactured with micrometer precision, but also economically – especially in large quantities. This is exactly where we at IBK Engineering come in. Our latest project shows how well thought-out product and process consulting not only saves costs, but also makes production more sustainable.
Initial situation: When machining reaches its limits
Our customer, a medical technology company, had a clearly defined goal: A thin-walled precision sleeve with a sheet thickness of just 0.1 mm was to be manufactured more efficiently in future – without compromising on dimensional accuracy and quality.
Previously, production was carried out by machining – a cost-intensive process that quickly becomes uneconomical for higher quantities.
The central question was:
“How can the production of precision parts with a wall thickness of 0.1 mm be made more economical?”
Our answer: With deep-drawing technology and a modular forming tool.
The solution: from the idea to scalable series production
With our tried-and-tested consulting and development process, we have consistently converted product manufacturing to thermoforming technology – with significant added value for our customer. The project went through four clearly defined phases:
- Phase: Analysis, consulting and virtual process development
We began with an in-depth product analysis. We evaluated the manufacturability of the sleeve under the requirements of thermoforming technology and analyzed relevant characteristics such as tolerances, material behavior and subsequent use in the overall medical technology system.
This was followed by intensive product consultation, during which we worked with the customer to make design adjustments. The aim was to design the component in such a way that it is ideally “deep-drawable” – without compromising its functionality.
With the help of FEM simulations, all process steps were mapped virtually. This enabled us to identify and optimize critical points at an early stage. The result: a resilient, sustainable product design with optimum forming properties – a “best fit”. - Phase: Tool construction and validation through pilot series
Based on the simulation results, we developed a modular forming tool that can be used not only for the current sleeve, but also for future variants. The tool was validated by means of “0” series production, in which we produced the first real components and compared them with the required specifications. - Phase: Process integration and fine-tuning at the customer
We supported the commissioning process in close coordination with the customer. Our experts optimized the process parameters directly during the customer’s validation – for maximum process reliability, short cycle times and consistently high component quality. - Phase: Scaling and development of variant concepts
Finally, we developed several concepts for series production – including the possible integration of other article groups with similar requirements. The modular structure of our tool system allows future components to be integrated into the line quickly and economically.
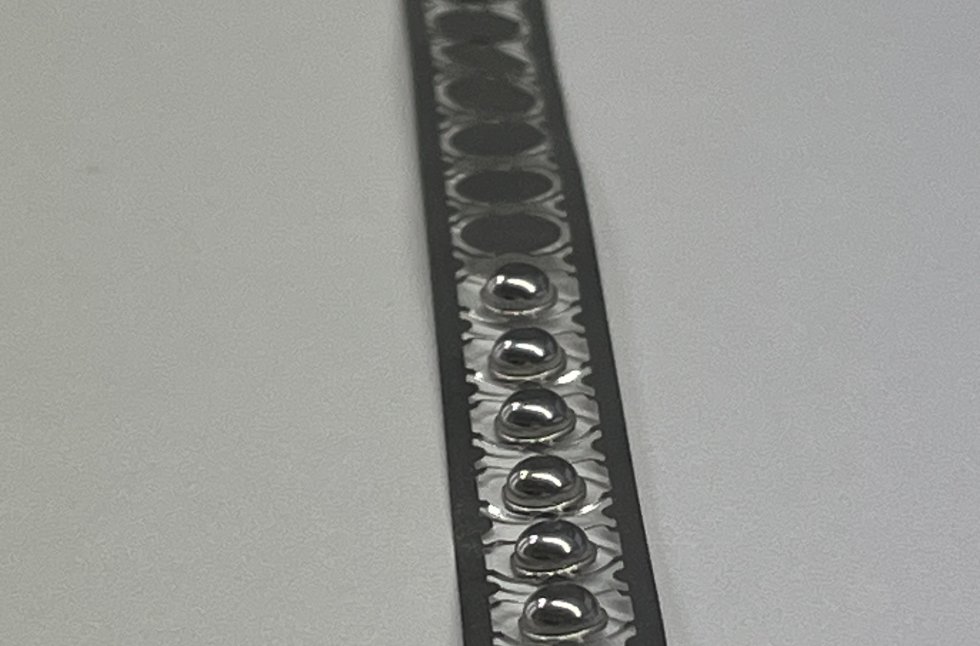
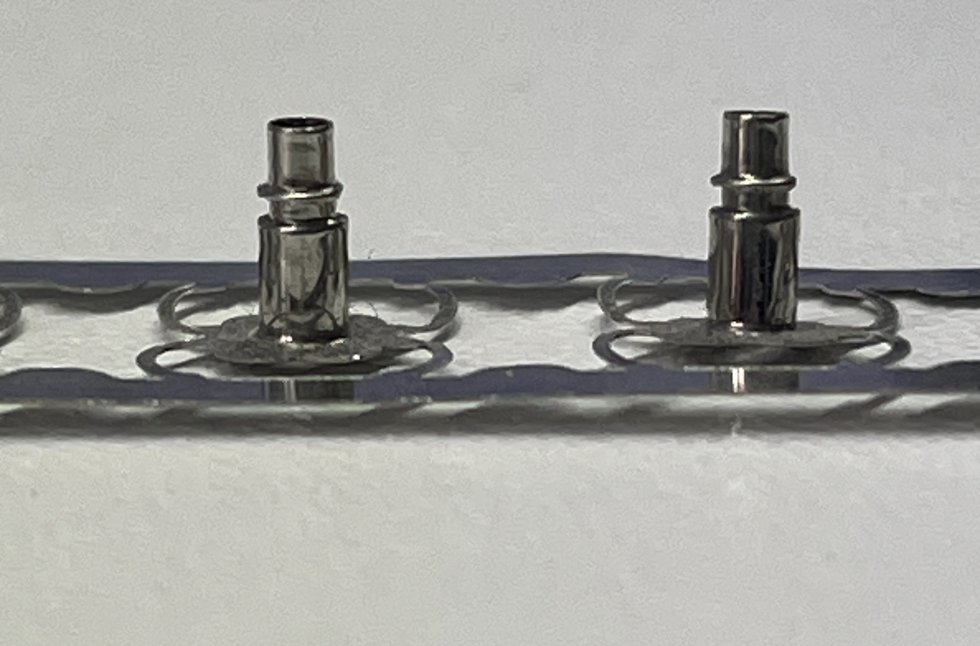
Why the switch to deep-drawn parts has paid off:
- Up to 35% lower article costs by switching to thermoforming technology
- Reduced material usage and fewer rejects
- Shorter cycle times and better scalability
- Simulation-based safety even before tool production
- Sustainable production through modular tool systems
Frequently asked questions about deep-drawing technology for precision parts:
Is deep-drawing technology for precision parts with extremely thin sheet thickness reliable?
Yes. Thanks to modern FEM simulations and our experience in toolmaking for complex geometries, we can manufacture even thin-walled precision parts – e.g. 0.1 mm sheet thickness – with process reliability and repeat accuracy and with the tightest tolerances.
How can deep-drawing technology save costs in the production of components?
Forming technology replaces cost-intensive machining processes, reduces material loss and significantly lowers unit costs – especially for medium to large batch sizes. At the same time, energy consumption per component is reduced.
Can one forming tool be used for several components?
Absolutely. Our modular tool systems can be flexibly adapted. This means that product families or variants can be integrated into existing processes with little effort.
How long does it take to develop a deep-drawing tool for a precision part?
The development time varies depending on the complexity and number of simulation iterations. Thanks to our standardized approach and digital process planning, we can significantly shorten development times. In addition, our partner companies and our well-maintained supplier network to Asia ensure optimal procurement.
Conclusion
The transformation to deep-drawing technology was a complete success: our customer benefits from a stable, sustainable production process and significant cost savings. And best of all, the solution is scalable – for future variants or completely new components.
Any questions?
Do you have questions about your product or process? Our experts will be happy to advise you. Simply get in touch!