Wie eine kleine Hülse Großes bewirkt – und wir mit unserem Know-how bis zu 35 % Artikelkosten einsparen.
In der Medizintechnik zählt jedes Detail. Bauteile müssen nicht nur mikrometergenau gefertigt sein, sondern auch wirtschaftlich – besonders bei hoher Stückzahl. Genau hier setzen wir bei IBK Engineering an. Unser jüngstes Projekt zeigt, wie durchdachte Produkt- und Prozessberatung nicht nur Kosten einspart, sondern auch die Fertigung nachhaltiger gestaltet.
Ausgangssituation: Wenn Zerspanung an ihre Grenzen stößt
Unser Kunde, ein Unternehmen aus der Medizintechnik, hatte ein klar umrissenes Ziel: Eine dünnwandige Präzisionshülse mit einer Blechdicke von nur 0,1 mm sollte künftig effizienter gefertigt werden – ohne Kompromisse bei Maßhaltigkeit und Qualität.
Bisher erfolgte die Produktion zerspanend – ein kostenintensives Verfahren, das bei höheren Stückzahlen schnell unwirtschaftlich wird.
Die zentrale Frage lautete:
„Wie kann die Fertigung von Präzisionsteilen mit 0,1 mm Wandstärke wirtschaftlicher gestaltet werden?“
Unsere Antwort: Mit Tiefziehtechnik und einem modular aufgebauten Umformwerkzeug.
Der Lösungsweg: Von der Idee bis zur skalierbaren Serienfertigung
Mit unserem erprobten Beratungs- und Entwicklungsprozess haben wir die Produktfertigung konsequent auf die Tiefziehtechnik umgestellt – mit signifikantem Mehrwert für unseren Kunden. Das Projekt durchlief dabei vier klar definierte Phasen:
- Phase: Analyse, Beratung und virtuelle Prozessentwicklung
Zu Beginn stand eine tiefgehende Produktanalyse. Wir bewerteten die Herstellbarkeit der Hülse unter den Anforderungen der Tiefziehtechnik und analysierten relevante Merkmale wie Toleranzen, Materialverhalten und die spätere Verwendung im medizintechnischen Gesamtsystem.
Darauf folgte eine intensive Produktberatung, in der wir gemeinsam mit dem Kunden konstruktive Designanpassungen vornahmen. Ziel war es, das Bauteil so zu gestalten, dass es ideal „tiefziehbar“ ist – ohne seine Funktionalität zu gefährden.
Mithilfe von FEM-Simulationen wurden alle Prozessschritte virtuell abgebildet. So konnten wir kritische Stellen frühzeitig erkennen und optimieren. Das Ergebnis: ein belastbares, nachhaltiges Produktdesign mit optimalen Umformeigenschaften – ein „best fit“. - Phase: Werkzeugbau und Validierung durch Nullserie
Basierend auf den Simulationsergebnissen entwickelten wir ein modulares Umformwerkzeug, das nicht nur für die aktuelle Hülse, sondern auch für zukünftige Varianten genutzt werden kann. Die Werkzeugvalidierung erfolgte durch eine „0“-Serienfertigung, bei der wir erste reale Bauteile produzierten und mit den geforderten Spezifikationen abglichen. - Phase: Prozessintegration und Feinjustierung beim Kunden
In enger Abstimmung mit dem Kunden begleiteten wir den Prozess zur Inbetriebnahme. Unsere Experten optimierten die Prozessparameter direkt während der kundenseitigen Validierung – für maximale Prozesssicherheit, geringe Taktzeiten und stabil hohe Bauteilqualität. - Phase: Skalierung und Entwicklung von Variantenkonzepten
Abschließend erarbeiteten wir mehrere Konzepte für die Serienfertigung – inklusive möglicher Integration weiterer Artikelgruppen mit ähnlichen Anforderungen. Der modulare Aufbau unseres Werkzeugsystems erlaubt es, auch künftige Bauteile schnell und wirtschaftlich in die Linie zu integrieren.
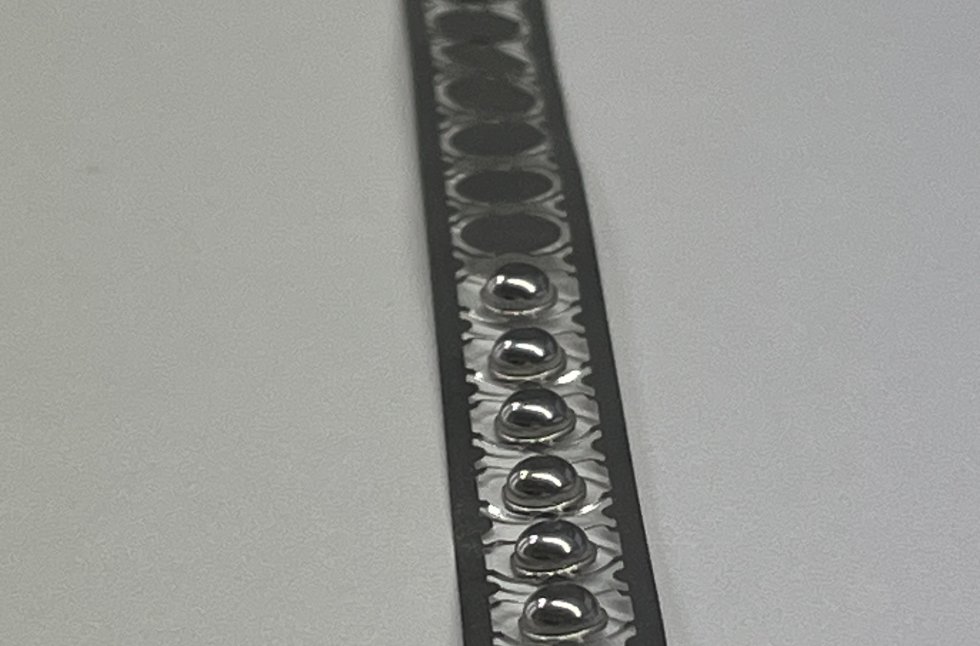
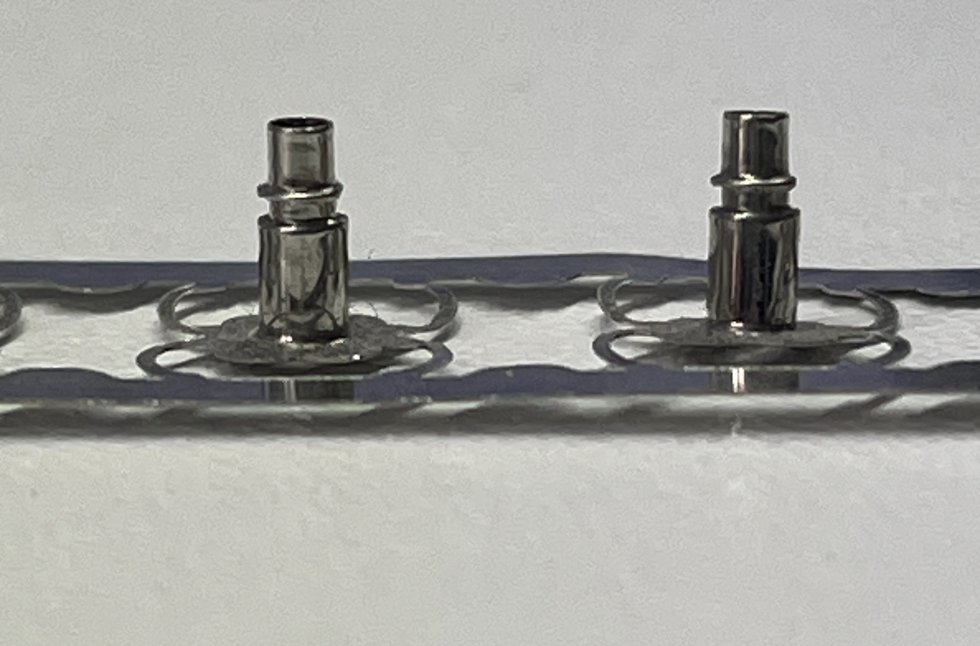
Warum sich der Umstieg auf Tiefziehteile gelohnt hat:
- Bis zu 35 % geringere Artikelkosten durch den Wechsel zur Tiefziehtechnik
- Reduzierter Materialeinsatz und weniger Ausschuss
- Kürzere Zykluszeiten und bessere Skalierbarkeit
- Simulationsbasierte Sicherheit schon vor der Werkzeugfertigung
- Zukunftsfähige Produktion durch modulare Werkzeugsysteme
Häufig gestellte Fragen zur Tiefziehtechnik für Präzisionsteile:
Ist die Tiefziehtechnik für Präzisionsteile mit extrem dünner Blechdicke prozesssicher?
Ja. Dank moderner FEM-Simulationen und unserer Erfahrung im Werkzeugbau für anspruchsvolle Geometrien können wir selbst dünnwandige Präzisionsteile – z. B. 0,1 mm Blechdicke – prozesssicher und wiederholgenau fertigen und das mit engsten Toleranzen.
Wie lassen sich durch Tiefziehtechnik Kosten bei der Fertigung von Bauteilen einsparen?
Die Umformtechnik ersetzt kostenintensive Zerspanprozesse, reduziert Materialverlust und senkt die Stückkosten signifikant – vor allem bei mittleren bis hohen Losgrößen. Gleichzeitig sinkt der Energieverbrauch pro Bauteil.
Kann ein Umformwerkzeug für mehrere Bauteile genutzt werden?
Absolut. Unsere modularen Werkzeugsysteme lassen sich flexibel anpassen. So können Produktfamilien oder Varianten mit geringem Aufwand in bestehende Prozesse integriert werden.
Wie lange dauert es, ein Tiefziehwerkzeug für ein Präzisionsteil zu entwickeln?
Je nach Komplexität und Anzahl der Simulations-Iterationen variiert die Entwicklungszeit. Durch unser standardisiertes Vorgehen und digitale Prozessplanung können wir Entwicklungszeiten deutlich verkürzen. Dazu sichern unser Partnerunternehmen und unser gut gepflegtes Lieferantennetzwerk nach Asien eine optimale Beschaffung zu.
Fazit
Die Transformation zur Tiefziehtechnik war ein voller Erfolg: Unser Kunde profitiert von einem stabilen, nachhaltigen Fertigungsprozess und signifikanten Kosteneinsparungen. Und das Beste: Die Lösung ist skalierbar – für künftige Varianten oder komplett neue Bauteile.
Noch Fragen?
Sie haben Fragen zu Ihrem Produkt oder Prozess? Unsere Experten stehen Ihnen gerne für eine Beratung zur Seite. Nehmen Sie dafür einfach Kontakt auf!